Politecnico di Milano
In una bella sera di inizio primavera, mi trovo al Mip, la Business school del Politecnico di Milano, per tenere una lezione sul sistema di produzione Toyota. La classe è composta da una quarantina di giovani tra i 30 e i 45 anni, che sono già al lavoro in azienda da circa 10 anni e che frequentano alla sera un master in un’affermata Business school. Comincio la lezione e, dopo un po’ di teoria, che è sempre noiosa, presento una delle evoluzioni più recenti del sistema Toyota, nota come Wcm (World Class Manufacturing). Allo scopo di suscitare l’interesse della classe, mi aiuto con alcuni esempi pratici sviluppati nelle fabbriche di auto della Fiat a partire dal 2005. Proietto sullo schermo varie fotografie di impianti e di posti di lavoro "prima e dopo” e un paio di filmati, tratti da Youtube, su come si assembla l’automobile. Si trattava di cose abbastanza nuove, ma che mi sembravano quasi normali, o almeno non sconvolgenti, per giovani manager che studiano in una Business school. Gli studenti invece restano molto impressionati e qualcuno è proprio esterrefatto. Mi dicono che non immaginavano assolutamente che le fabbriche si fossero evolute così tanto e soprattutto che la Fiat, la cui immagine in Italia è legata alle vecchie auto che si rompevano spesso, avesse fatto tali progressi.
Lo stupore contagia anche le persone che lavorano in imprese manifatturiere della Lombardia e del Veneto. In questi territori l’industria è spesso molto avanzata e sofisticata per quanto riguarda le singole macchine e i cicli di lavorazione, ma è ancora "vecchia” e tradizionale rispetto all’organizzazione del posto di lavoro, il flusso logistico, la sicurezza e il sistema di gestione. Alla fine della lezione c’è un fitto scambio di impressioni e a gran voce arriva la richiesta di andare a vedere di persona, tutti insieme, una "nuova” fabbrica di auto. Mi devo impegnare subito a chiedere a Fiat di consentirci una visita di gruppo, come Mip: a mia volta chiedo agli studenti di mettercela tutta per ottenere dalla loro azienda una giornata di permesso aggiuntivo. (Marzo 2010)
Fiat Mirafiori
Abbiamo ottenuto il permesso di visitare un’area del grande stabilimento di Mirafiori dove si produce la nuova Alfa Romeo Mito, modello di punta della gamma Alfa, un’auto che è un gioiellino a tre porte, di solito rosso fuoco o nero lucido, con una linea inconfondibile. Siamo accolti, in una chiara mattina di maggio, dal responsabile dell’area, da alcuni tecnici dello staff Wcm e da un giovane collaboratore, specialista di comunicazione.
Il responsabile, gentilissimo, in giacca e cravatta blu brillante, ci illustra gli elementi essenziali della nuova linea di produzione della Mito, che è la più moderna di Mirafiori sia per le tecnologie, in particolare quelle dello stampaggio lamiere, della lastratura della scocca e della verniciatura, sia per l’applicazione del Wcm, che si è concentrato sulla sicurezza, sull’ordine nel posto di lavoro, sulla qualità e in parte sulla logistica dei materiali lato linea.
Gli specialisti del Wcm.
Le persone più attive e coinvolte nell’innovazione sono i tecnici e gli specialisti del Wcm, alcuni dei quali sono presenti all’incontro e ci illustrano i risultati ottenuti. Questi tecnici si sono formati nei corsi tenuti dallo staff centrale del Wcm e poi sono diventati "Pillar leader” o membri del team di "Pillar”, cioè specialisti di un’area tematica dell’innovazione, come ad esempio la qualità, la sicurezza, la manutenzione specialistica, ecc.
Loro studiano le criticità principali della fabbrica relative al proprio tema e poi propongono delle innovazioni che, se approvate, vengono attuate con progetti mirati all’efficienza, alla sicurezza, al miglioramento della qualità. Il numero di progetti sviluppati è assai elevato e a prima vista incredibile rispetto al passato industriale italiano, di solito "paludoso e pigro”. Va detto che spesso si tratta di modifiche limitate, piccole, ma che sommate tra di loro producono molti miglioramenti e molti risparmi.
I suggerimenti dei lavoratori.
I lavoratori vengono informati dai cartelloni che sono presenti in tutta la fabbrica, frequentano corsi di formazione introduttivi e sono principalmente stimolati a partecipare attraverso i suggerimenti. I suggerimenti sono molto richiesti dal nuovo sistema per "migliorare le cose che non vanno” a partire dall’esperienza diretta di chi lavora quotidianamente sulla linea. Spesso sono idee semplici o ingenue, ma molte volte sono invece soluzioni geniali per problemi complessi, che a tavolino gli ingegneri non erano riusciti a immaginare oppure che non avevano "visto”. I suggerimenti sono numerosissimi, molte migliaia, e tendono a crescere man mano che cresce il numero e l’impegno dei progetti Wcm per migliorare il funzionamento della linea: è impressionante come tante idee vengano fornite gratis, in cambio di riconoscimenti simbolici o semplici gadget, rivelando una voglia di migliorare la qualità del lavoro e del prodotto molto vasta, diffusa e profonda tra i lavoratori.
L’organizzazione è ancora tradizionale.
Uno studente chiede quale sia la struttura organizzativa; dalla risposta si ricava che essa è ancora la vecchia struttura della Ute, con i capi turno e i capi linea, a cui sono stati affiancati gli staff del Wcm, con i pillar leader e i loro progetti. Dei team operai e del team leader si parla sottovoce, come di qualcosa di futuribile e anche un po’ misterioso.
L’automazione nella costruzione della scocca.
Finite le presentazioni si va finalmente a vedere la fabbrica. Ma gli spazi si svelano molto vasti per i miei "ragazzi”, abituati alle medie e piccole imprese lombarde, e ci sarebbe da camminare parecchio. Per fortuna interviene la nostra giovane guida, che ci fa salire su una specie di trenino turistico che ci conduce, comodamente seduti, a spasso per la fabbrica, che lui stesso ci spiega attraverso microfono e cuffie, come se stessimo visitando la città di Avignone o di Strasburgo sul trenino dei turisti. Gli ambienti si rivelano quelli tradizionali della grande fabbrica anni 60: capannoni molto alti, spesso bui e scuri, poco illuminati se non al montaggio, molto rumore, spazi immensi con grossi problemi di trasporto dei materiali. In lastratura e verniciatura ci sono le tecnologie illustrate prima; si tratta delle generazioni recenti di impianti automatizzati, anche se non sempre le ultime. L’automazione è ampia, anche se in qualche punto c’è ancora manualità; i compiti dei lavoratori sono principalmente di manutenzione e controllo dei robot di saldatura e verniciatura. In questi settori il Wcm si applica soprattutto come metodo di manutenzione e di controllo e miglioramento degli impianti.
La linea di montaggio.
Al montaggio invece gli effetti del Wcm sono molto più direttamente visibili: gli ambienti sono più chiari, puliti e luminosi e i posti di lavoro lungo la linea molto più ordinati e ben disposti. Sono spariti i mucchi di materiali gettati alla rinfusa a lato linea, non si vedono più i lavoratori andare a rovistare negli scatoloni per cercare i pezzi da montare sull’auto assegnata, non c’è chi corre o chiama il capo perché non trova il particolare giusto. Ci sono invece a fianco di ogni scocca i famosi "carrellini della spesa”, con sopra già "sequenziati” tutti e soli i pezzi da montare su quell’auto con gli optional previsti. Le operazioni di montaggio sono facilitate e meno faticose perché la scocca talvolta viene spostata a piano terra, talvolta viene alzata, talvolta viene piegata a 45° per facilitare il lavoro sottoscocca. I miei "ragazzi” sono colpiti dall’ordine e dalla buona sistemazione delle cose, dal flusso preciso dei pezzi, dalle tute pulite degli operai, dalle protezione di sicurezza degli impianti. Tutte cose che contrastano con l’idea di fabbrica tradizionale che avevano in mente: sporca, confusa, faticosissima, piena di pericoli, di trappole e di disordine.
Tuttavia gli sguardi degli studenti esperti individuano ancora molti montaggi manuali e non assistiti da robot disponibili sul mercato: sono montati manualmente i cristalli anteriore e posteriore, il montaggio delle parti meccaniche è solo in parte robotizzato, il cruscotto e la plancia non sono preassemblati e moltissime operazioni sono fatte con attrezzi generalisti, come gli universali e comunissimi avvitatori a batteria, che paiono l’attrezzo più diffuso. Insomma, c’è molto "fai da te” su tante postazioni di lavoro. In generale si intuisce che il Wcm si è concentrato sugli sprechi più evidenti e diffusi, come il camminare per cercare i materiali, gli spostamenti ripetuti dei materiali, le cose posate per terra in disordine, i pericoli più evidenti, le perdite di olio e i guasti delle macchine, gli scarti e i rifiuti, e così via. Si vedono i risultati della caccia agli sprechi: è stata l’età d’oro del Pillar "cost deployment”, come si dice nel gergo del Wcm. Inoltre i lavoratori sembrano concentrati sul proprio singolo posto di lavoro, non sembra esserci molta collaborazione, si parlano poco anche tra loro, c’è distanza dai capi.
Luci e ombre del cambiamento.
Quando usciamo c’è una grande euforia tra i "ragazzi”, si ha l’impressione di avere visto qualcosa di profondamente nuovo e di poco conosciuto. Il nuovo sembra un misto di tecnologie evolute e di un nuovo ruolo dell’intelligenza delle persone, anche degli operai. Quelli che però sono più esperti di fabbrica, fanno notare che l’organizzazione e i ruoli formali delle persone sono cambiati poco, la struttura della Ute ha quasi vent’anni, il lavoro in team si fa solo nei gruppi di progetto, gli specialisti Wcm sono ancora i protagonisti assoluti, la partecipazione è dichiarata ma di fatto ancora debole. (Maggio 2010)
Pomigliano
A Napoli, in novembre, per noi del nord è ancora quasi estate. Ci arrivo con una delegazione sindacale che sta facendo una ricerca europea importante e che è stata invitata nella fabbrica della Fiat Panda. Una fabbrica che è stata da poco completamente ristrutturata con un grosso investimento di qualche miliardo di euro. Il paese di Pomigliano è di fatto una periferia confusa, ingolfata e caotica, dove i campi, i frutteti e gli orti si mescolano a case, fabbriche, negozi, strade e svincoli autostradali. La vecchia fabbrica dell’Alfa Sud mi appare immensa, con i suoi oltre due milioni di metri quadri, ma ora è per l’88% chiusa e abbandonata. La nuova fabbrica della Panda occupa solo il restante 12% dello spazio. La vecchia palazzina degli uffici della Direzione è stata chiusa e mi sembra anche murata. In pratica è un rudere abbandonato: il direttore e tutto lo staff direzionale si sono trasferiti dentro il capannone del montaggio per essere più vicini agli operai.
I dirigenti con la stessa tuta degli operai e l’"acquario”.
Il Direttore dunque ci riceve non già nel suo ufficio, che è semplice, tutto vetri e piccolo come quelli dei suoi collaboratori, ma in un’ampia sala riunioni dove ci viene offerto l’immancabile caffè napoletano. Mentre bevo il caffè, mi dice che si è laureato negli anni 70 al Politecnico di Milano e mi chiede notizie di come è posizionato oggi l’Istituto di meccanica dove ha studiato in gioventù. Lo guardo incuriosito e me lo immagino giovanissimo, con giacca, cravatta e occhiali alla Gino Paoli, come si usava allora, mentre si prende il diploma di laurea nelle austere aule del Politecnico, con i professori in toga ed ermellino; invece ora vedo davanti a me un uomo maturo con la tuta bianca e grigia degli operai di linea, con il nome scritto sul petto e pure con le scarpe antinfortunistiche ai piedi, vestito esattamente come tutti gli altri. Siamo noi visitatori che siamo vestiti strani e diversi. Lui coglie la curiosità nei miei occhi e subito mi racconta come è stata chiusa la palazzina direzionale e come si è deciso di mettere il gruppo dirigente in un ”acquario”, cioè in uno spazio attiguo alle linee di montaggio completamente trasparente, in modo che tutti si vedano e possano dialogare più facilmente. Poi mi racconta anche che il suo stile di direzione è basato sul confronto aperto e diretto con tutti i ruoli senza dare troppa importanza preconcetta ai "gradi”. La riunione principale è infatti al mattino: un folto gruppo di collaboratori diretti, ma anche di team leader, di tecnici delle varie aree, di operai e di rappresentanti sindacali a rotazione si riunisce in direzione per discutere in un paio di ore dei problemi emersi nelle giornate precedenti e per decidere insieme il da farsi, cioè le principali azioni correttive. Con questo stile ha gestito la completa riorganizzazione della fabbrica e il lancio del grande investimento nella nuova Panda con il rientro di molti cassintegrati e con il modello più evoluto di Wcm. Pomigliano è, infatti, alla fine del 2012, l’applicazione più evoluta, completa e innovativa del Wcm e del nuovo modello organizzativo di Fiat Group. Infatti, da qualche mese il sistema di audit interno ha attribuito la qualifica di "Oro” allo stabilimento. Tuttavia mi accorgo subito che i sindacalisti, ma forse anche il direttore, sono ancora più fieri del giudizio molto lusinghiero dato alla fabbrica da una giuria di tecnici specializzati tedeschi (proprio loro, i tedeschi!) che ha riconosciuto Pomigliano come uno degli stabilimenti più avanzati in Europa, addirittura meglio di quello di Lipsia, ritenuto il non plus ultra delle fabbriche di auto in Germania.
Quali sono le grandi novità di Pomigliano? A me sembra di capire che ci siano molti aspetti dell’innovazione applicati in questa fabbrica, ma che in sostanza le tantissime cose siano riconducibili a due filoni.
Le nuove linee di produzione.
Nel corso della visita alla fabbrica, questa volta a piedi, si osserva con facilità il primo filone: cioè le nuove stazioni di lavoro e la nuova linea. Per costruirle si è fatto tesoro di tutte le esperienze del Wcm e delle tecnologie produttive nell’intero mondo Fiat e Chrysler. Ci mostrano molti accorgimenti nei reparti di lastratura, verniciatura e montaggio che sono frutto di anni di studi e di esperienze per migliorare la qualità del prodotto, l’efficienza del lavoro e per ridurre la fatica. I risultati si vedono nei montaggi dentro la vettura, nel "marriage” tra meccanica e scocca, nel pavimento della linea che avanza con la scocca, nei supporti per il convogliamento delle parti pesanti, nell’accuratezza dei pre-assemblaggi a lato linea, ad esempio del cruscotto, nel flusso dei materiali perfettamente just in time, e così via. Ci sono poi i pavimenti pulitissimi e le ultime generazioni di sistemi automatizzati per la lastratura, la verniciatura e per il montaggio dei cristalli e delle parti meccaniche. Tutto questo ha voluto dire molti investimenti, ma anche molti studi, molto scambio di esperienze, molte verifiche di funzionalità, di efficienza e qualità. Queste novità mi impressionano, ma non mi stupiscono: c’è tanto impegno, tanta fatica e tanti denari, ma alla fine si tratta dell’innovazione ordinaria che ci dovremmo aspettare da una grande azienda globale.
Il team operaio.
A metà visita, mi presentano una signora responsabile della formazione aziendale: le chiedo che cosa sta facendo e quali iniziative abbia avviato. Per rispondere mi conducono in un ampio laboratorio di fianco e parallelo alla linea, dove ci sono moltissimi cartelloni didattici e delle scocche di vetture mezze smontate. È il "pilotino”, laboratorio sperimentale di formazione.
Spiegandomi l’uso di questo "pilotino”, viene fuori la vera novità di Pomigliano, che è il nuovo sistema di organizzazione del lavoro basato sui team operai e sul team leader. Il team operaio è certamente un salto, sia rispetto alla tradizione Fiat sia rispetto alla più diffusa cultura industriale italiana.
A me anzi pare una rottura netta con tutto il Novecento. La soluzione della delega e della responsabilizzazione del team operaio, collegata alla centralità del team leader è in effetti una forte alternativa ai gravi difetti della gerarchia di fabbrica. Il team operaio e il team leader, inteso come un "primus inter pares”, sono in sostanza responsabili e dotati di molta autonomia su un tratto di linea con sei postazioni di lavoro che viene detto "dominio”. Nel dominio essi possono ruotare, si aiutano a vicenda, propongono i miglioramenti, fanno la produzione. Il sistema dei team è stato adottato da anni in molte fabbriche di auto come Toyota, Volkswagen, Bmw e in molti altri ambienti aziendali, ma in Italia non era mai stato applicato con tanta coerenza e completezza come a Pomigliano. Il team leader, mi dice il direttore, non deve essere un "capetto”, ma una sorta di operaio specializzato del Ventunesimo secolo che coordina i suoi compagni di lavoro in base alle sue competenze professionali.
Il team partecipa alla progettazione della linea.
Il processo di creazione dei team leader e dei team è durato vari mesi e si è svolto in parallelo all’investimento e alla costruzione della nuova fabbrica. In primo luogo sono stati scelti, con metodi strutturati, i team leader tra gli operai migliori, circa 150 persone, attraverso incontri e colloqui. Essi sono stati prima coinvolti in un processo formativo, sia sul Wcm sia su aspetti tecnici, e poi sono stati inseriti nella progettazione delle postazioni di lavoro per la parte di linea a cui erano stati destinati. La progettazione della nuova linea è stata effettuata non più a tavolino ma in un laboratorio, simulando tratti sperimentali di linea (il "pilotino” appunto) che riproducevano in parte le condizioni reali di ciascun dominio (cioè le sei postazioni di lavoro che in futuro saranno lo spazio di lavoro di ciascun team operaio).
Sul "pilotino” sono passati in seguito anche gli operai di ciascun team che si sono così impratichiti della nuova postazione di lavoro socializzando con i compagni di team e con il team leader. Il racconto della responsabile della formazione va molto per le lunghe e devo chiuderlo a un certo punto; in sostanza, il principale vantaggio è stato che questo processo di formazione ha consentito di apportare moltissime modifiche ai compiti e alle sequenze di montaggio partendo dai suggerimenti degli operai. Inoltre sono state apprese e diffuse le metodologie ergonomiche e di saturazione dei tempi adottate da Fiat (il cosiddetto Ergo-Uas). In breve, c’è stato un coinvolgimento e una partecipazione diretta del team leader e del team alla progettazione dei posti di lavoro. Prima di lasciare la fabbrica riesco a fare un’ultima domanda ai giovani che mi accompagnano: ma chi è veramente il team leader? Mi rispondono che secondo loro è uno specialista di processo che coordina i compagni sia per la gestione del flusso ordinario sia per i suggerimenti, la crescita della polivalenza e della rotazione nel team.
Nella mia mente osservo che tutto questo però ha consentito di ridurre drasticamente la gerarchia di fabbrica: infatti, al di sotto dei capi Ute ci sono solo i supervisori capiturno e poi i team leader.
A me è sembrato che sia stata questa "rivoluzione del team operaio”, insieme alla completa riorganizzazione dello stabilimento, a creare il clima da prato verde che si respira a Pomigliano e a rendere molto alto l’entusiasmo dei lavoratori e molto basso l’assenteismo registrato negli ultimi mesi. Ma accanto a questi aspetti positivi non bisogna dimenticare che a Pomigliano, come nel resto delle fabbriche Fiat, ci sono ancora centinaia di lavoratori in cassa integrazione che attendono di rientrare al lavoro e per i quali il "prato verde” è ancora lontano. È questo ancora un punto di grave sofferenza su cui i sindacalisti insistono continuamente. (Novembre 2012)
Grugliasco
La nuova Maserati è in una fabbrica chiamata popolarmente ex Bertone perché era sin dagli anni Sessanta un laboratorio di auto particolari e di lusso. È situata nella vasta periferia di Torino, sulla strada delle montagne della Val di Susa. Alle 8 del mattino, a giugno, il sole è già alto anche a Torino e fa risplendere il verde carico dei prati che punteggiano la campagna e le Alpi Cozie che svettano non troppo lontano. La Maserati non è enorme come Mirafiori, non è neanche un grande parallelepipedo colorato come Melfi, ma è fatta di un gruppo di capannoni classici col tetto bombato e semicilindrico, che sono stati rimessi a nuovo e ridipinti perché Grugliasco sta diventando una fabbrica del "polo del lusso”.
La prima sorpresa è l’accoglienza: niente badge né guardie giurate, siamo ricevuti dal direttore in persona, un simpatico ingegnere tedesco che per prima cosa ci presenta lei. Si tratta della Ghibli un’auto di gran lusso, bellissima, vestita di un nero lucente e accattivante, con sedili e arredi interni da fantascienza.
Dopo la presentazione il direttore mi apre la portiera lato guida della Ghibli e mi fa cenno di accomodarmi. Sono imbarazzato, non mi è mai capitato di salire su un’auto del genere. Sono un po’ a disagio e mi scuso: io sono cresciuto con la vecchia 500, al massimo sono stato sulla Giulietta. Il direttore capisce, si mette a ridere, mi fa sedere sul sedile lato passeggero mettendosi lui stesso al posto guida; accende subito il motore e lo porta rapidamente su di giri. A "soli” 2.000 giri il rombo è forte, come una mitraglia, e mi sembra di stare alle prove di Formula 1. Gli chiedo che razza di motore abbiano messo nella Ghibli! Il direttore, che deve essersi abituato a questa domanda, mi apre il grande cofano nero. Ecco svelato uno dei segreti della Ghibli: c’è dentro un motore Ferrari, classicissimo, con la scritta "Ferrari” così grande che mi toglie ogni dubbio e ogni voglia di indagare oltre. Deve essere veramente un’auto velocissima, oltre che di lusso.
Un’auto di lusso costruita con il Wcm.
Camminando verso la fabbrica mi spiegano che la Ghibli e l’altro modello vanno molto bene, le vendite corrono forte e la Maserati si sta qualificando come una "quasi” Ferrari. È un "alto di gamma” che però deve essere costruita in decine di migliaia di pezzi e quindi deve essere più "industrializzata” della Ferrari, non può essere fatta in modo quasi artigianale come a Maranello. L’idea quindi è stata quella di usare l’organizzazione del Wcm e le migliori tecniche produttive sperimentate nelle fabbriche Fiat più avanzate, come ad esempio a Pomigliano. Si tratta evidentemente di una sfida, di una grossa sfida. Infatti il Wcm è nato per la produzione di massa e a flusso teso e deve allora essere adattato a un prodotto un po’ diverso. Per vincere questa sfida, la fabbrica, dove la produzione è appena iniziata ed è in fase di avvio, è diventata una specie di grande laboratorio sperimentale. Giriamo sulla linea di assemblaggio nelle fasi iniziali e vediamo che in ogni tratto, detto "dominio”, perché è assegnato a un team di sei operai più il team leader, ci sono varie persone che parlano tra loro e provano e riprovano le operazioni di montaggio. Sono i tecnici della qualità che insieme agli operai e al team leader verificano le tecniche di montaggio e cercano la soluzione adatta a un sistema industriale avanzato.
Mi illustrano diversi accorgimenti, soluzioni particolari e veri e propri trucchi del mestiere che, prova e riprova, hanno lo stesso obiettivo: garantire una qualità massima del prodotto, evitando gli sprechi di ogni genere e operando con modi industriali e con le tecnologie più evolute. Mi dicono che questo obiettivo si può raggiungere usando lo stesso metodo di Pomigliano; cioè coinvolgere ampiamente gli operai di linea nei suggerimenti per il miglioramento, formare i team leader sia come specialisti tecnici, sia come "leader” del gruppo e, infine, far dialogare tutto il team operaio con gli specialisti delle tecnologie e della qualità.
Gli operai e il cambiamento: luci e ombre.
Mi fermo a parlare con alcuni operai appena rientrati dalla cassa integrazione e venuti qui da Mirafiori: che ne pensate di questo vostro coinvolgimento nella progettazione del vostro posto di lavoro? Mi dicono che è all’inizio, sono "spaesati”, un po’ increduli e che sospendono il giudizio. Nella vecchia Mirafiori si era pagati "non per pensare ma solo per lavorare”. Si doveva ubbidire e basta. Qui sembra tutto molto diverso, si è pagati anche per pensare, addirittura per trovare nuove soluzioni tecnico-organizzative. Certo, la fabbrica è più pulita, molto sicura, con tecnologie nuovissime, ma bisogna imparare, formarsi sul Wcm, dialogare coi compagni e col team leader e poi anche con gli specialisti, riflettere sul lavoro che si fa. Chiedo loro che bilancio fanno tra prima e dopo: la prima risposta tenta un equilibrio tra vantaggi e svantaggi, ma poi il discorso diventa meno cauto e si sbilanciano. È evidente che il "nuovo lavoro” attrae, che avrà pure i suoi aspetti negativi ma è più coinvolgente, più interessante e alla fine molto più motivante.
D’altra parte però c’è il problema del cosiddetto "stress”: bisogna stare sempre molto attenti, non ci si può distrarre, l’errore è in agguato. E poi ci sono i tempi; è vero che la progettazione ergonomica dei posti di lavoro riduce la fatica fisica, ma l’abolizione delle attività prive di valore aggiunto "ha riempito il tempo”, non ci sono più quelle attività secondarie, come cercare il pezzo giusto, che ti consentivano di distrarti un po’. Qualcuno percepisce questo cambiamento come intensificazione dei ritmi, che invece sono gli stessi.
L’ufficio formazione in mezzo all’officina che aiuta a risolvere i problemi.
Camminando lungo la linea mi fanno scoprire molte altre particolarità e specificità tecniche della fabbrica, elaborate nel solco delle idee del Wcm. Il discorso diventa molto lungo, perché la varietà delle soluzioni è di grande interesse: non c’è spazio per raccontarle tutte qui. L’ultima sorpresa, soprattutto per me che sono anche un professore, è l’Ufficio formazione. Questo Ufficio è stato un perno centrale del lancio della nuova fabbrica perché ha sviluppato il complesso percorso formativo dei team leader che sono la spina dorsale della produzione Maserati. Se la fabbrica ora va bene lo si deve anche al Piano Formativo dei team leader, durato molti mesi. È stato adottato all’incirca lo stesso percorso di Pomigliano: primo passo formazione tecnica e sul Wcm, poi coinvolgimento nella progettazione e messa a punto della linea, poi formazione sociale e coinvolgimento nell’avvio del team operaio.
Ma adesso che la produzione si è avviata dov’è, e che cosa fa, l’Ufficio formazione? Lo incontro in mezzo all’officina, in spazi chiari e luminosi, accanto alla linea di montaggio. Hanno qualche tavolo, moltissimi cartelloni, i manuali tecnici e del Wcm, molti computer e ovviamente varie attrezzature e "accrocchi” per simulare i posti di lavoro. Mi spiegano che, adesso, oltre a ripetere i cicli formativi per i nuovi lavoratori che rientrano dalla cassa integrazione, fanno "formazione sui problemi”. In pratica significa che quando ci sono problemi di non facile soluzione nel team o con i tecnici, puoi rivolgerti ai formatori che ti aiutano a risolverli. Ovviamente loro non ti suggeriscono la soluzione, perché non c’è l’hanno, ma ti suggeriscono un metodo di indagine che verosimilmente ti aiuterà a trovarla. Mi informo su cosa pensino nell’Ufficio della differenza tra il lavoro di prima, svolto negli uffici della palazzina impiegati, e quello di adesso, in officina. Risposta: si impara molto di più e si fa un’analisi del fabbisogno formativo sul campo, che risulta molto, molto più approfondita.
Il tempo è volato, quando usciamo il sole è alto nel cielo e la luce è molto forte e brucia: ci guardiamo negli occhi e ci chiediamo se alla fine decollerà davvero il "polo del lusso”.
Ci diciamo che da un lato i lavoratori sono molto entusiasti e impegnati e che il clima è di grande fervore, ma che, dall’altro lato, è evidente che molti non si sono ancora abituati al nuovo sistema, non lo hanno ancora capito e qualcuno ancora si sente estraneo. E poi ci sono i nuovi problemi e le nuove fatiche. Però chiudiamo con un po’ di ottimismo: "Vedrai che ce la faranno”. (Giugno 2013)
Melfi
La fabbrica di Melfi è come una grandissima astronave, un grande cubo a strisce colorate, decollata dal Nord industriale e atterrata nella campagna assolata e disabitata della regione Basilicata. I campi intorno sono molto vasti e coltivati di solito a grano, verdi d’inverno e gialli d’estate, ma non si vedono case di contadini in giro. La gente sta su, nei paesi arroccati sulle colline e deve fare molta strada in auto per venire in fabbrica.
La fabbrica è nata già nuova, come "fabbrica integrata” agli inizi degli anni 90. In vent’anni ha prodotto più di cinque milioni di autovetture (sempre la Punto e la Ypsilon) ed è già una gloria industriale dell’Italia, anche per i suoi elevati livelli di efficienza. I lavoratori sono quasi gli stessi delle origini, sono entrati giovani, tutti ventenni, e ora sono in gran parte quarantenni: qualche anno fa c’è stato un grosso conflitto sindacale per cambiare gli orari di lavoro, progettati per i ventenni ma non più adeguati quando ci si fa una famiglia.
Una jeep prodotta in Italia su una linea Wcm.
A Melfi hanno costruito la "nuova” fabbrica chiudendo metà della vecchia. In altre parole, una delle due linee di produzione della Punto è stata trasformata in una linea completamente nuova per la produzione di 2 nuovi Suv: la Jeep Renegade, che è stata presentata in marzo al salone di Ginevra, e la nuova 500X.
Il Suv è un prodotto molto affermato sul mercato, ma è completamente nuovo per le fabbriche italiane della Fiat; così a Melfi hanno dovuto imparare in fretta e mettercela tutta per tenere i tempi dell’investimento.
La nuovissima linea di produzione dei due Suv utilizza tutte le esperienze e le innovazioni accumulate a Pomigliano, a Grugliasco e nelle altre fabbriche americane del gruppo Fiat, e cerca anzi di fare ancora meglio.
Perciò il direttore dello stabilimento, che ci fa la prima spiegazione della fabbrica, non perde molto tempo e procede per differenze da Pomigliano. Tra l’altro è lo stesso ingegnere laureato al Politecnico di Milano che ci ha accolto l’anno scorso nella fabbrica di Pomigliano. Ci ha accolto col suo solito stile di coinvolgimento allargato, in mezzo a molti collaboratori, tutti giovani e alcune donne. Ci siamo presi in giro a vicenda poiché io e lui risultiamo essere gli unici con i capelli grigi, anzi lui appena grigi e io bianchi, in mezzo a tanti giovani. Va detto che a Melfi anche i sindacalisti sono più giovani del resto d’Italia e non hanno ancora i capelli grigi.
L’apprendimento organizzativo da Pomigliano a Melfi.
Le novità adottate a Melfi e illustrate dal direttore si possono riassumere in due filoni o gruppi principali. In primo luogo la progettazione della linea di produzione nel suo insieme e delle varie stazioni di lavoro, è stata ancora più precisa, evoluta e in un certo senso "ossessiva” (è una parola mia) nel cercare soluzioni di lavoro che siano allo stesso tempo efficienti, di massima qualità del prodotto, ed ergonomiche per i lavoratori, cioè comode e non dannose sul lungo periodo. Per arrivare a questo risultato c’è stato in primo luogo una lunga verifica, attuata per mezzo di sistemi ergonomici evoluti, delle postazioni di lavoro per azzerare le mansioni "rosse” e ridurre al minimo quelle "gialle”. Poi c’è stato uno studio tecnico degli attrezzi, dei materiali e dei supporti di vario genere, anche informativi. Quando andiamo sulla linea, infatti, ci fanno vedere sia tanti attrezzi disegnati ad hoc per procedere a specifiche azioni, sia vari accorgimenti inediti per ridurre le mansioni troppo faticose e, infine, un display per ogni stazione di lavoro.
Il display supporta gli operai con informazioni specifiche e consente loro di comunicare con il sistema centrale e con i compagni di lavoro e il team leader. Consente anche di fermare la linea quando necessario e questa è una novità assoluta per le fabbriche Fiat. Intere fasi di montaggio poi sono state progettate con soluzioni innovative, come ad esempio il "marriage” della meccanica con la scocca, totalmente automatizzato.
La progettazione congiunta prodotto/processo tra i team leader e i progettisti.
Ma la novità più grossa che veramente mi ha stupito è che la fase di formazione dei team leader non si è applicata come a Pomigliano solo sulla progettazione della linea di lavoro, e quindi delle postazioni e del processo produttivo, ma ha riguardato anche la fase di progettazione del prodotto. Su questa progettazione congiunta prodotto/processo il direttore insiste molto, ma io lo seguo benissimo perché è un chiodo fisso dell’insegnamento che facciamo al Politecnico di Milano, da molti anni e con tanti colleghi.
In pratica, i circa 300 team leader, dopo la formazione usuale, sono stati mandati a gruppi, per due mesi a Torino, vicino ai progettisti dei nuovi Suv, per verificare con loro il disegno del prodotto e per controllare quale fosse la facilità di montaggio delle varie parti della nuova auto, infine per suggerire modifiche e variazioni. Tutto ciò con lo scopo di rendere più agevole e più efficiente il montaggio e per ridurre i possibili errori. Questa opera di revisione del progetto originario per assicurare la fattibilità e la facilità di costruzione, sviluppata insieme da progettisti e team leader, ha prodotto all’incirca 2.000 modifiche al progetto base, di cui alcune centinaia di un certo rilievo, definite di tipo strutturale. Sono numeri eccezionali. I benefici si vedranno soprattutto sulla qualità delle vetture finali, ma anche sulla efficacia e la buona qualità del lavoro in linea. Come ricercatore e professore sono entusiasta: finalmente si realizza un principio dei nostri insegnamenti al Politecnico.
Un’organizzazione basata sui team operai.
In conclusione, l’organizzazione della nuova linea di Melfi riprende e sviluppa l’organizzazione snella basata sui team e i team leader di Pomigliano. C’è un’evoluzione nel senso che il percorso di professionalizzazione dei team leader è stato più ampio, diversificato e approfondito. Non so come si svilupperà, anzi sono molto curioso di vedere l’evoluzione di questa nuova figura, ma a me sembra che il team leader sia qualcosa di nuovo, definibile come l’operaio specializzato del mondo attuale: un leader di un piccolo gruppo di operai, certamente, ma anche un grande specialista di una fase del processo con elevate capacità tecniche e di soluzione di problemi.
Luci e ombre.
Anche a Melfi emergono alcuni punti difficili del cambiamento. In primo luogo la questione dei tempi nei montaggi, su cui ci sono percezioni diverse. Molti apprezzano bene i positivi effetti dell’ergonomia, che riduce la fatica, e le postazioni ben bilanciate nei tempi, altri percepiscono la riduzione delle attività prive di valore aggiunto (tempi "meno porosi”) come un’intensificazione dei ritmi, che invece non c’è. Poi c’è la maggiore attenzione e la crescita dell’impegno cognitivo, vissuto come "stressante” da alcuni e come motivante da altri. Sono temi molto nuovi su cui bisognerà studiare. (Febbraio 2014)
Riflessioni finali nel viaggio di ritorno
Melfi è la nostra ultima tappa. Torniamo verso il Nord in auto, una Fiat Cubo, con Alberto e Anna. Si procede a velocità abbastanza bassa, di crociera, perché la Cubo non assomiglia in niente alla Ghibli Maserati e c’è tempo per parlare tra noi. Tutto il nostro chiacchierare si può riassumere in due idee. La prima è che abbiamo davanti a noi sistemi produttivi che sono completamente nuovi rispetto a quelli in cui siamo cresciuti: non basta più la parola "post fordismo”, ora è tutto diverso. Oggi lavorare vuol ancora dire "fare”, ma poi vuol dire anche pensare, comunicare con gli altri, ragionare insieme e trovare soluzioni nuove. Le barriere tra ingegnere e operaio stanno sciogliendosi e le conoscenze fluiscono dall’uno all’altro, come in un girotondo: certe volte si fanno addirittura degli esperimenti insieme. La seconda idea è che allora c’è moltissimo da fare, perché la cultura del paese Italia è invece rimasta molto indietro: bisogna aggiornare gli italiani, tutti, ma in particolare i gruppi dirigenti, le élite politiche e sindacali; la fabbrica e il lavoro sono cambiati profondamente. E poi bisogna adeguare tutti gli altri sistemi che girano intorno alla fabbrica: il rapporto tra fabbriche e città, la scuola, la cultura, l’informazione e anche il sindacato.
Luciano Pero
Viaggio di Luciano Pero nelle nuove fabbriche Fiat, dal 2010 al 2014, da Mirafiori a Melfi
problemi di lavoro
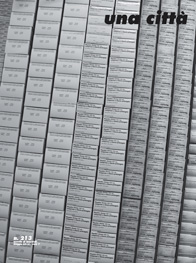
Una Città n° 213 / 2014 maggio
Articolo di Luciano Pero
DA MIRAFIORI A MELFI
In viaggio nelle nuove fabbriche Fiat, da Mirafiori, dove alla linea non si vedono più operai cercare pezzi e però restano molti montaggi manuali, a Pomigliano, dove il direttore è in tuta come gli altri operai, ci sono team operai e il “pilotino”, un laboratorio sperimentale di formazione, e poi a Grugliasco e Melfi, dove i team leader sono stati coinvolti anche nella progettazione. Di Luciano Pero.
Archivio
PARTECIPAZIONE E INNOVAZIONE
Una Città n° 178 / 2010 Ottobre
Realizzata da Barbara Bertoncin
Realizzata da Barbara Bertoncin
Luciano Pero è docente di Organizzazione per il Mip Politecnico di Milano e professore a contratto di Sistemi Organizzativi presso la Facoltà di Ingegneria dei Sistemi sede di Como. Si interessa di innovazione organizzativa, architetture dei sistemi infor...
Leggi di più
LA PAGINA 7, CHE MANCA...
Una Città n° 186 / 2011 luglio 2011
Realizzata da Barbara Bertoncin
Realizzata da Barbara Bertoncin
Edi Lazzi è responsabile Quinta lega Fiom di Mirafiori, Alberto Cipriani è responsabile Fim di Mirafiori; Luciano Pero è docente di Organizzazione per il Mip Politecnico di Milano e si interessa di innovazione organizzativa, relazioni industriali e mercat...
Leggi di più
ORARIO DI LAVORO PANDEMIA E DIGITALIZZAZIONE
Una Città n° 291 / 2023 marzo
Realizzata da Barbara Bertoncin
Realizzata da Barbara Bertoncin
Luigi Campagna è docente alla Graduate School of Management (GSoM) del Politecnico di Milano. Svolge consulenza per la progettazione di nuovi modelli organizzativi e di sistemi di knowledge management. Luciano Pero è docente alla GSoM del Po...
Leggi di più
I TEAM DI POMIGLIANO
Una Città n° 231 / 2016 maggio-giugno
Realizzata da Barbara Bertoncin
Realizzata da Barbara Bertoncin
Luciano Pero è docente di Organizzazione al Mip Politecnico di Milano. Si interessa di innovazione organizzativa, architetture dei sistemi informativi, relazioni industriali e mercato del lavoro. Il libro di cui si parla nell’intervista &egra...
Leggi di più
IL TEAM E IL TEMPO
Una Città n° 201 / 2013 Marzo
Realizzata da Barbara Bertoncin
Realizzata da Barbara Bertoncin
Luciano Pero è docente di Organizzazione per il Mip Politecnico di Milano. Si interessa di innovazione organizzativa, architetture dei sistemi informativi, relazioni industriali e mercato del lavoro; Anna Ponzellini è studiosa di organizzazi...
Leggi di più